Computational Fluid Dynamics Study of the Effects of Secondary Flow in 90-degree Pipe Elbow Erosion
Computational fluid dynamics of particle-laden fluid flows through a 90-degree pipe elbow were completed at Reynolds numbers 1,000 and 10,000; for different elbow curvature ratios of 1.0, 1.5, and 2.5; and for particles with different Stokes numbers of 0.05, 0.1, 0.5, 1.0, 5.0, and 10.0. The particles were modeled using a Lagrangian approach and assuming a one-way interaction with the fluid. The modeling was performed using COMSOL Multiphysics®, specifically its CFD and Particle Tracing Modules. The physical model had three main sections, the pipe connected to the elbow inlet, the pipe connected to the elbow outlet, and the elbow itself. The inlet and outlet pipes were long enough to make sure the eliminate any boundary condition effect on the elbow flow. A mesh sensitivity analysis was performed to minimize mesh numerical error. The Finnie model was used when calculating the resulting erosion in the elbow. There were two scenarios in the study. For the first, the particles felt drag from the primary (or the axial) flow as well as from the secondary fluid flows in the elbow. For the second, the secondary fluid flow in the 90-degree bend was artificially suppressed from the particle drag, thus the particles only felt the flow in the axial direction of the flow. These simulation scenarios were made to analyze how suppressing the secondary flow could cause less erosion in the 90-degree bend of the pipe when compared to the particles feeling both the primary and secondary flows of the fluid. The results show that secondary flows do not affect much the erosion when the particle Stokes number is high (close to 10). On the other hand, when the Stokes number is less than one, a significant 20% to 50% reduction on the erosion is observed. This erosion reduction depends on the Reynolds number and radius of curvature. For even smaller Stokes numbers no erosion was found in certain cases since the particles tend to follow precisely the flow, avoiding wall contact. Interestingly, for the particular case of the turbulent flow, the comparison between the full flow model and the model with no secondary flow reveals that when the curvature ratio is increased there is little difference in the amount of erosion. In addition to observe the erosion itself, particle impact velocity, angle of incidence, and erosion location were also examined to learn more about the secondary flow effect on the particle erosion. This study serves as a preliminary insight to the effects of curvature ratio, Stokes number, and Reynolds number in relation to the significance of secondary fluid flow on erosion in a 90-degree pipe elbow. Although this is somewhat comprehensive study, additional work is necessary in order to acquire further information on the relationships of secondary fluid flow and erosion in pipe elbows.
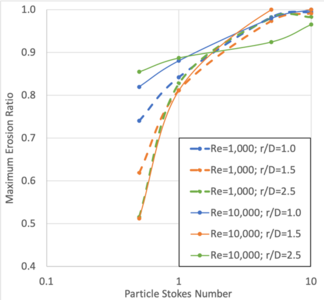