Virtual Prototyping of UV-LED Based Point-of-Use Water Disinfection Unit
Water disinfection using UV light is a well-known technology. Conventionally, mercury based cylindrical lamps are used, however, recently LED based UV lamps have emerged on a commercial scale. These devices hold several advantages compared to the conventional lamps, e.g. being mercury-free, no initialization time and the possibility of on/off operation. This makes UV-LEDs well-suited for point-of-use water disinfection. At this point the UV-LEDs still have a lower wall plug efficiency compared to the conventional lamps but offers extended possibilities for innovative reactor designs. Thus, to ensure competitiveness the UV-LED technology must rely on a more efficient design. When designing the UV flow-through reactor several elements must be addressed, such as geometrical design of flow chamber, properties of reactor walls, placement, number and type of UV-LEDs as well as geometry and properties of quartz glass window separating the LEDs and the flow chamber. Under a given set of water flow rate and water UV absorbance the reactor design results in a distribution of UV doses based on the combined effect of flow pattern and fluence rate distribution. It is this distribution of UV doses that determines the reactor efficiency in terms of microbial inactivation, and thus it is the reactor property to be optimized. A conventional approach to design optimization would be physical testing of prototypes, however, given the large numbers of degrees of freedom in the design this would be an expensive and time-consuming approach. Therefore, virtual prototyping using numerical simulation offers an attractive alternative in order to reduces cost and time. This study demonstrates the use of COMSOL Multiphysics® for virtual prototyping of a UV reactor. The model uses the Laminar Flow interface, the Geometrical Optics interface and the Particle Tracing for Fluid Flow for computing the flow pattern, fluence distribution and dose distribution, respectively. In this way the particles (resembling microorganisms) are transported through the reactor using the velocity field of the flow model by drag forces while accumulating UV dose according to the UV fluence rate field. A number of reactor designs, reactor wall properties, LED positions, quartz glass dimensions and water UV absorbance are evaluated to investigate the effect on reactor efficiency. The results highlight the strong interaction of velocity field and fluence rate distribution on the resulting dose distribution and underlines the necessity of a careful design of the UV reactor to avoid low-dose-paths.
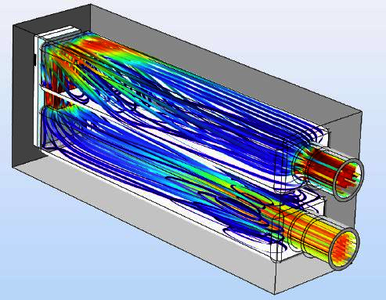
下载
- christensen_presentation.pdf - 1.93MB
- christensen_abstract.pdf - 0.03MB