Genetic Algorithm Based Multi-Objective Optimization of Electromagnetic Components using COMSOL® and MATLAB® Software
INTRODUCTION
The global energy infrastructure is comprised of a variety of power magnetic devices (PMDs) which include motors, generators, transformers, inductors, actuators, relays, etc. In the field of power engineering, and particularly in the design of PMDs, modern advances are targeted at reducing system losses, mass, volume, and cost, while simultaneously increasing power capability, reliability, and large-scale manufacturability. Achieving these competing objectives in modern applications requires advanced methods for optimal design of PMDs. These include computationally efficient device models in conjunction with state-of-the-art global optimization techniques.
In this work, an EI-core actuator is designed to obtain the tradeoff between competing volume and loss objectives. The actuator is shown in Figure 1, and is made of a stationary E-core wrapped with a coil of conducting wire and a movable I-core. The AC/DC Module of COMSOL® software is used in 2D for electromagnetic field analysis coupled with a genetic algorithm (GA) toolbox implemented in MATLAB [1,2]. It is noted that in this straightforward application, a Magnetic Equivalent Circuit (MEC) based modeling approach may also be used [3]. The volume of the actuator is obtained using a parameterized geometry, the inputs of which are considered as design parameters for the GA. The losses are obtained based on the DC resistance of the coil.
The design should also satisfy constraints such as minimum electromagnetic force, maximum current density, limit the aspect ratio and expected packing factor for manufacturing reasons, and disregard designs with excessive volume and power loss. With the exception of the airgap length (chosen based on the manufacturing limits), all dimensions and the material types are obtained using the outlined methodology.
USE OF COMSOL® SOFTWARE During the design process, the design parameters are associated to the geometry, winding structure, and material information, and are provided as population members of a GA generation. The design model obtains these parameters and conducts the field evaluations for the purposes of calculating the constraints (e.g. force) and objectives (i.e. volume and loss). Within COMSOL Multiphysics® software, a Parametric Sweep study is set up with specific combinations, wherein the values are set via the LiveLink™ for MATLAB® Module. The AC/DC Module calculates the results (e.g. force on the I- core) and feeds them back into MATLAB® software.
RESULTS An electromagnetic actuator capable of delivering 2500 N of force is designed. The GA is initialized with 200 population members and run for 200 generations. In Figure 2, the resulting Pareto-Optimal fronts [2], obtained using both the COMSOL Multiphysics- and MEC-based models are shown. The parameters for Design 50, obtained using COMSOL software, are given in Figure 4; the design geometry and flux density distribution is presented in Figure 3.
CONCLUSION A multi-objective design of an actuator using COMSOL® and MATLAB® software is presented. The Pareto- Optimal front agrees well with that obtained using an MEC-based design optimization. The methodology is sufficiently general to be expanded to the variety of PMD applications outlined above. A detailed analysis, study, results, and discussion will be presented in the full paper.
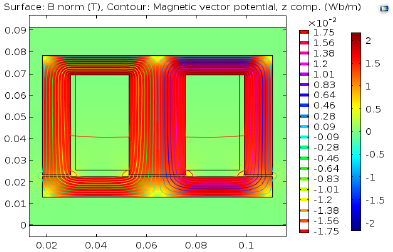
下载
- subbiah_presentation.pdf - 0.89MB
- subbiah_poster.pdf - 0.9MB
- subbiah_paper.pdf - 0.57MB
- subbiah_abstract.pdf - 0.27MB