Flow Optimization of a MVHR Combined with an Exhaust Air Heat Pump by Means of CFD Simulation
In the framework of the Austrian FFG project SaLüΗ!, a compact mechanical ventilation system with integrated micro-heat pump was developed. The aim was a high level of prefabrication and a compact design allowing for installation also in small flats, e.g. into the façade. Due to the compactness, the system must be optimized as far as pressure drop, flow homogeneity and sound emissions are concerned.
Preliminary CFD modelling and optimization of the system is investigated, concentrating on the supply air duct. The COMSOL Multiphysics® software was used. The model assumes isothermal, incompressible flow through the duct.
The aim was to analyse and compare the inlet air flow homogeneity in front of a straight and V-styled condenser. Different 2D heat exchanger models were calibrated with respect to pressure drop and inlet velocity profile. A preliminary comparison with experimental data is carried out for both pressure drop and 2D transitional flow around a bluff body, by employing EES as well as results of Lourenco and Shih for the near wake of a circular cylinder at Re = 3900.
Four different 3D models are compared: an homogeneity coefficient based on standard deviation is introduced and calculated for the normal velocity component to the condenser inlet surface. The results show that a very compact system can result in a lack of homogeneity of the air flow through the heat exchangers, which can only be slightly reduced by splitting the condenser in two parts.
Further developments are necessary to improve, refine and extend the validity of the model.
Condenser modelling: in the COMSOL® software, when anisotropic porous media is employed, the coefficients of the tensor are related to the global Cartesian coordinate system of the entire model, which refer to the spatial frame. This limits the flexibility of the model, for example in the case in which the heat exchanger does not follow the spatial coordinates. A solution would be to define a relative coordinate system related to the porous media domain inlet, by employing a Base Vector System and use it with Curvilinear Coordinates interface. However, for the moment it is not possible to implement this solution.
Turbulent flow around the obstacle: High and Low Reynolds number turbulence models must be compared also via a three-dimensional benchmark flow, e.g. flow around a small aspect ratio cylinder, where no periodic vortex shedding takes place, but a strong three-dimensional wake dominates the flow. Experimental data for Re=60000 are available in Adamarola (2006). Reynolds Stress Models should also be considered in future works.
Flow optimization: other methodologies for the evaluation of the performance can be used. Standard deviation is known to be sensible to outliner values, and might not be always a robust deviance estimator. More samples can also be used for having a better picture of the mesh influence on the punctual velocity. A consistent mesh refinement is necessary at the inlet of the condenser and around the compressor.
Blockage and under-pressure effects on cylinder wake structure must be examined, as well as ventilator outflow and inflow velocity profile.
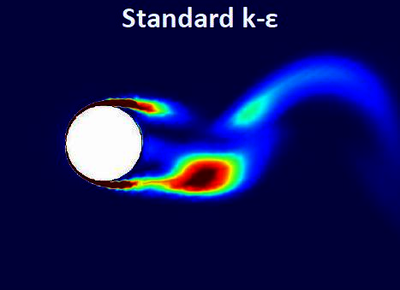
下载
- ochs_presentation.pdf - 1.46MB
- ochs_paper.pdf - 0.75MB
- ochs_abstract.pdf - 0.02MB