Design and Simulation of Piezoelectric Ultrasonic Micro Motor
Micro machined motors are a recent development in the domain of electrical machines. Compared to the conventional electromagnetic motors, micro machined motors offer high torque at lower speed, and are compact in nature. This makes them suitable for applications in the field of microsatellite, biomedical, micro robot, automobile, and auto focusing camera. The present work describes the design and simulation of piezoelectric micro motors. These motors use inverse piezoelectric effect. They consist of a stator and a rotor. The stator includes a segmented piezoelectric ring. When electrical voltage is applied to this piezoelectric ring, it deforms. By appropriately choosing the magnitude and frequencies of the voltages applied to the stator, the stator can be made to deform in the form of a traveling wave, which travels along the outer circumference of the stator at different frequencies. Here, the stator vibrates at ultrasonic frequencies. The rotor sitting atop the stator is propelled by the wave. Because of the friction at the contact area between the stator and the rotor, the ultrasonic vibration of the stator is converted into rotational motion of the rotor. In the present work, the stator with piezoelectric ring is designed with ten wave number operation. This is achieved by choosing appropriate polarization pattern of the segment of the piezoelectric ring and proper electrode configuration of the ring. The design and analysis of the stator is the main step in the designing of these motors. Accordingly the mechanics and dynamics of this complex stator are carried out using the COMSOL Multiphysics 4.2a.The designed stator of the piezoelectric ultrasonic micro motor is as shown in Figure1. The Eigen frequency analysis resulted in different mode shapes and the corresponding natural frequencies. Tenth natural mode occurred at the natural frequency of 52 kHz. Fig. 2 shows the tenth mode shape of the stator of the piezoelectric ultrasonic micro motor by performing the Eigen frequency analysis. Next the frequency analysis performed on the stator of the piezoelectric ultrasonic micro motor. In this analysis, the coefficient of Rayleigh damping has been included. The coefficient of Rayleigh damping has been calculated from the Eigen frequency analysis results. From this analysis the resonant frequency was observed to be 52 kHz with 10 wave numbers. The maximum crest of the each wave in Z direction is 0.372 micro meter as shown in Fig. 3. Also carried out here, is the transient analysis. It is observed that the stator reaches the steady state after 1.8 msec. This analysis is a crucial in optimizing the motor design. Traditional piezoelectric motors suffer from a fundamental limitation of bidirectional polarization of piezoelectric ring. This problem has been solved by using uniformly polarized piezoelectric ring. In this work, it was found that, by using a higher grade piezoelectric material, greater displacement of stator can be achieved. Consequently rotor can generate higher torque increasing the efficiency of the motor. Another important finding is that increasing the supply voltage amplitude increases the stator displacement. The relationship is linear.
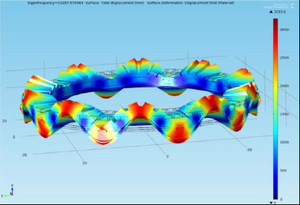
下载
- patel_paper.pdf - 0.54MB
- patel_abstract.pdf - 0.2MB