CFD modelling of a carbonation reactor
The transition to sustainable production includes the reduction of fossil material usage. Vegetable oil can be used as a reagent to form polyurethane by epoxidation through three major reaction steps, epoxidation, carbonation, and aminolysis. Many attempts have been made to model these reactions, but they generally do not account for the changes in material properties in terms of spatial coordinates. The spatial information related to the material properties can lead to better models, where the material properties change significantly based on the concentration or shear stress. Computational Fluid Dynamics can be an excellent method to describe the processes, even in three dimensions. The major changes during the three reactions steps occur in the case of viscosity, and density—the viscosity changes in magnitude, which have a significant effect on the flow field. The understanding fo these flow field is crucial to ensure the safe operation of the device. The flow-related dead zones can lead to thermal runaway in case of exothermic reactions, which can be prevented with a detailed simulation, including the spatial dependent changes. In this study, the carbonation part of a polyurethane production process was investigated. A 2D model of the system was developed and validated based on physical measurements. The main challenge was to model the spatial coordinate dependent viscosity changes within the system. The detailed model includes the component balances, as well as the concentration, and time-dependent viscosity and density changes. We also created a 3D model of the system, and the results are compared to the 2D simulations. The primary aim of this study was the detailed modelling and validation of the carbonation vessel.
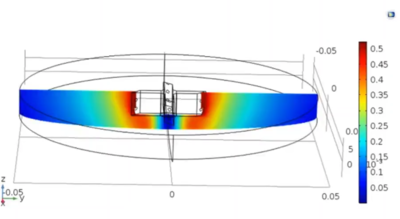