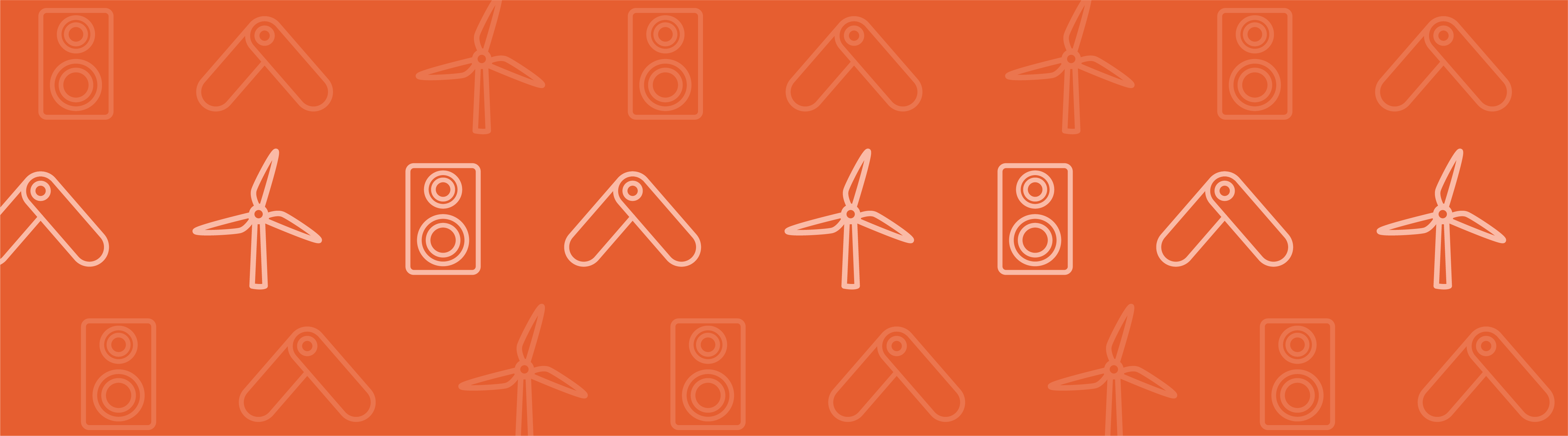
In these days of globalization, keeping the world connected is imperative. Information needs to pass as freely and quickly as possible in order to keep markets up-to-date with the latest news and to ensure that commerce can be conducted without hindrance (at least of the technical kind). So what do you do – look to the sky? The answer is no; in fact, 99% of this information is carried by undersea cables. These unsung heroes sit at the bottom of the sea. There they are buffeted by the high pressures and general movement of the surrounding water, and the rough terrain they lay upon. Even so, they provide instantaneous messaging between countries and peoples of different cultures. How do subsea cables withstand the stresses they are subjected to?
The latest issue of COMSOL News touches on this subject, with reports on JDR Cables. This is a company based out of the UK that designs and manufactures subsea umbilical systems of cables and reelers for oil and gas and renewable processes. They’ve been doing this for years, but increased requirements for quality and cost controls has led them to use modeling for their designs.
These subsea cables are not simple. They often contain a number of different wires of varying sizes, with different purposes in mind, as part of the cable package. These wires are all wound together within thick armature shells made of material tough enough to withstand the undersea environment. Once the cables have been manufactured, they are then wound onto large reels or spindles, placed onto a boat and then wound up and down as part of the laying process. Together with the harsh environment of the sea and wind, the cables also have to withstand the tensile forces that the cables are subjected to as part of the reeling process.
These subsea cables are not simple.
How JDR was able to simulate this is explained in the COMSOL News article. Part of their challenge was that they identified over 3,000 localized regions of high contact within the cable package. But once they, and their COMSOL Certified Consultant, Continuum Blue, were able to achieve this, they found their models cost half as much as physical testing, with further reductions in manufacturing costs.
Comments (0)